Whether you are building a bookshelf, a kitchen island, or a birdhouse, choosing the right material can make all the difference.
If you’ve ever worked on a woodworking project, you may have encountered MDF and plywood and may wonder which one would be the most suitable for your needs. You’re not alone in this conundrum as many woodworkers have found themselves stranded at this very same crossroads.
In this article MDF Vs Plywood comparison, we’re going to explore the properties, advantages, and limitations of MDF and Plywood in detail and try to figure out which is the best choice for your project.
So grab a cup of coffee, sit back, and let’s get started.
What is MDF?
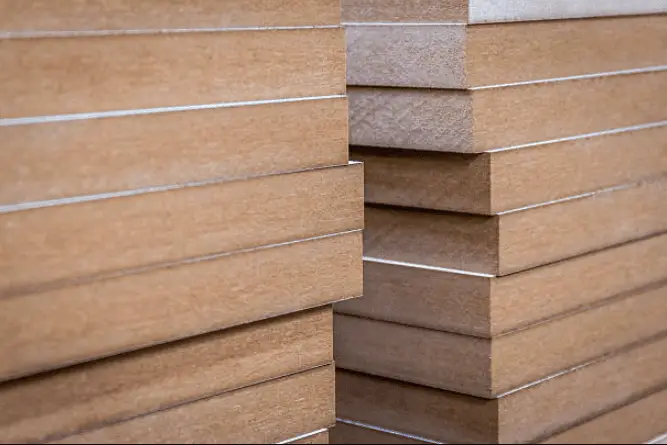
Medium-Density Fiberboard or MDF as it’s fondly referred to is a manufactured material created by combining sawdust and wood shavings with resin. It’s derived from recycled wood waste collected at mills. Instead of letting these wood mill byproducts go to waste, they are engineered to create a composite material that is both cost-effective and versatile.
And, let’s not forget about its environmental impact – using MDF helps reduce the amount of waste in landfills and makes the most of resources that would otherwise go unused.
Due to its uniform surface, MDF is hugely sought-after for furniture and cabinetry. It can be sanded and painted to perfection so it’s an ideal choice for large-scale projects as it won’t warp or shrink when exposed to changing temperatures and humidity.
The wood is often overlooked for its more glamorous counterparts but doesn’t let its humble appearance fool you. MDF packs a punch with its consistency, stability, and versatility.
As you plan your woodworking project, keep MDF in mind as an affordable and dependable substitute for solid wood. It is an excellent choice that won’t disappoint when it comes to performance and price.
What Makes MDF Tick
Let’s delve into the unique features that make MDF so versatile and dependable.
1. Strength
A major factor that decides the quality of the material is its internal bond strength. This is essentially the strength of the adhesive binding the fiber together, and this has a huge impact on how sturdy and long-lasting your MDF board will be.
The ability of MDF to withstand different levels of stress is measured by two key attributes – modulus of rupture and modulus of elasticity.
The modulus of rupture is a measure that gauges the strength and capacity of the MDF to resist breaking or rupturing while the modulus of elasticity measures its ability to resist deformation elastically.
2. Consistency
Medium-Density Fibreboard (MDF) is known for its impressive uniformity in appearance and quality.
It has become a very popular choice due to its consistent light-brown color maintained even when it is produced in large batches.
This ensures that all products created using the wood have the same superior quality, hence it is excellent for those who are looking for consistent results.
3. Susceptibility To Water Damage
MDF is not suitable for direct contact with water or high humidity as it may swell and warp easily. It is more prone to water damage than other types of wood so it must be kept away from these conditions.
If the material is exposed to such elements, it may expand and warp. Consequently, it’s essential to take necessary precautions for preservation.
Interior applications are ideal for Medium-Density Fiberboard as they can be shielded from moisture better. Even so, it’s imperative to take proper measures to guard the item against water damage that may occur.
4. Stability
MDF is known for its stability which is one of its key advantages over solid wood. Due to its engineered composition, it has a more consistent density and structure than solid wood.
This makes it less prone to warping, twisting, or cracking when exposed to changes in temperature and humidity. With its stability, MDF can be shaped into various forms, so it’s a popular choice for furniture and cabinetry.
5. Cost-Effective Wood
Man-made wood is an attractive choice for cost-conscious builders. This can help them to stretch their budget while still achieving quality results.
The manufacturing process for MDF is highly efficient; this helps to keep production costs low and the resulting material is also generally less expensive than solid wood.
6. Extremely Smooth Surface
One of the standout features of MDF is its incredibly smooth surface. Unlike solid wood with visible knots, grain patterns, and other imperfections, Medium-Density Fiberboard has a very smooth appearance.
It is ideal for a variety of applications that require a slick, seamless finish like built-in cabinetry or wainscoting.
This smooth surface also makes the wood an excellent choice for projects where precise cuts and joints are needed.
7. No Grain
Medium-Density Fiberboard is a composite material that has no grain like natural wood. For those of us who love the natural look of wood, the absence of grain in MDF may seem like a drawback. But for others, it’s a feature that sets MDF apart from its natural wood counterparts.
The lack of knots and grain in MDF makes it easy to saw.
Advantages of MDF Over Plywood
- MDF is indeed a budget-friendly option. It is a cost-effective alternative to more expensive types of wood like solid hardwoods or high-end plywood.
- It has a uniform density throughout the board, whereas plywood may have inconsistent thickness and density.
- The board is best for interior use.
Limitations
Medium-Density Fiberboard is not as durable as solid wood and tends to chip and crack if subjected to stress from heavyweight. Its smooth surface also means it’s not ideal for projects that require a natural or rustic look.
The high density and adhesive properties of MDF put extra strain on cutting tools leading to a shorter lifespan.
To minimize tool wear, use sharp blades and make cuts slowly and steadily. It’s also important to note that some specialized blades such as those made from carbide are better equipped to handle the demands of cutting MDF.
While MDF is an inexpensive material to use for woodworking, its resin may contain harmful fumes. It’s important to consider the potential health hazards linked with UF resin or dust derived from it before using MDF for wood items.
Urea-Formaldehyde resin is a binding agent that holds the fibers together; it releases a volatile organic compound that can be harmful to human health if inhaled. The gas can irritate the eyes, nose, throat, and lungs.
When To Use MDF
Medium-Density Fiberboard (MDF) is the perfect material for projects that require a smooth and polished finish. Because of its versatility and ease of use, it is ideal for interior trim, cabinet doors, furniture, and even other applications where strength and durability are not needed.
It is best for furniture like shelves and flooring due to its smooth surface and uniform texture. MDF is also great for decorative projects and wainscoting due to its ability to be cut into various shapes and sizes.
In addition, wood is often used in door frames and theater set construction due to its stability and affordability.
When Should You Not Use MDF?
MDF should not be used in areas where it will be constantly exposed to moisture and humidity; this can cause swelling and other damage.
Furthermore, the board mustn’t be used for exterior applications because it is not suitable for outdoor exposure and will not withstand the elements.
Instead, consider using a more moisture-resistant material such as solid wood for these applications.
Finally, MDF should also be avoided in applications where strength and durability are critical like in load-bearing walls. The reason for this is that the board is not as strong as other types of wood.
What is Plywood?
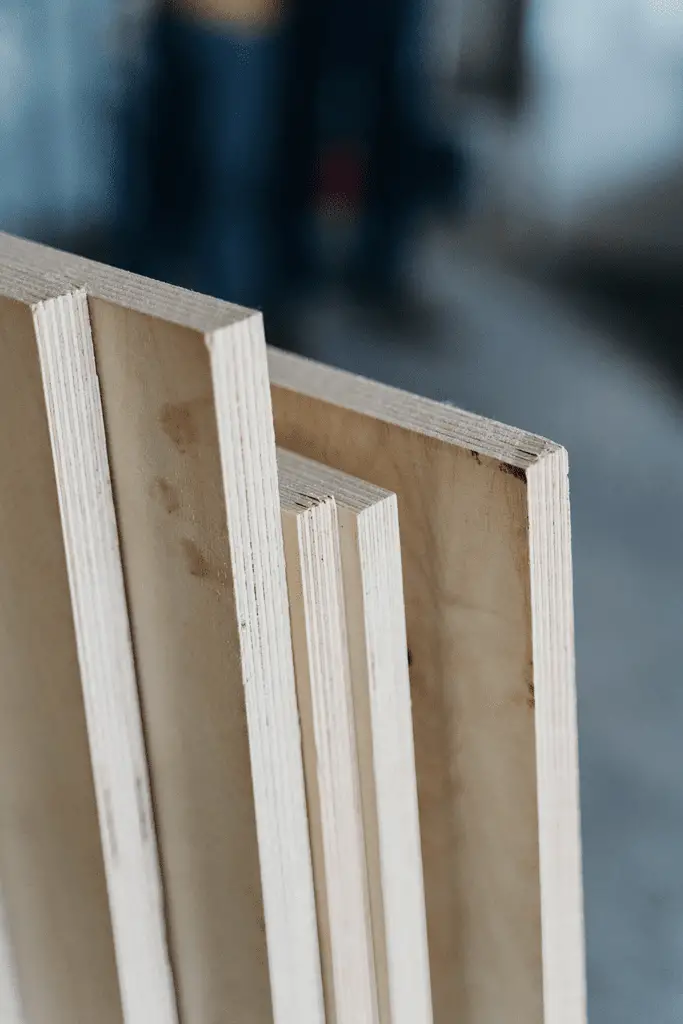
Plywood is an incredible material extensively used in a wide range of applications. Its creation involves the layering of thin wood veneer sheets which are then tightly joined together utilizing resin, heat, and pressure to form a stronger and more resilient material.
What Makes Plywood Tick
Plywood is one of the most versatile building and woodworking materials around. But what makes plywood so special? From its construction to its properties, let’s take a look at what makes plywood tick.
1. High Strength-To-Weight Ratio
The thin veneer sheets’ layering creates a much stronger but lightweight material. Plywood offers both strength and lightness so it is an outstanding option for many construction projects.
Also, it provides an admirable strength-to-weight ratio allowing it to be used in furniture making and other places that need long-lasting materials.
2. Resistance To Cracking and Splitting
The man-made wood is also very resistant to cracking and splitting, hence it is suitable for use in areas where it will be exposed to moisture like in projects that involve roofing or flooring.
The tight joining of the veneer sheets makes it much less likely to split or crack over time.
3. Low Cost
Another advantage of plywood is it is economical. Compared to other woodworking materials, plywood is relatively inexpensive making it a good choice for wood furniture where budget is a concern.
Due to its affordability, this material is an optimal selection for multiple construction tasks.
4. Excellent Screw-Holding Power
Plywood stands out among other materials for projects involving screws because of its exceptional screw-holding strength.
The securely layered veneers ensure that all screws remain firmly joined together, which prevents furniture parts from coming apart over time.
5. Versatility
Plywood is one of the most versatile building materials out there. Its versatility stems from the fact that it can be cut into different shapes and sizes, making it perfect for a wide range of applications.
It can be applied in many areas – from formwork and designer furniture to other applications like floor coverings and even interior paneling.
Whether you need to create a sturdy shelving unit, build a kitchen cabinet, or construct a wooden floor, plywood can provide the perfect solution.
Advantages of Plywood Over MDF
- Plywood is harder than MDF.
- Plywood’s cross-grained structure provides better dimensional stability.
- Plywood of higher quality often looks and feels much more attractive.
- Plywood is the preferred material for any external application which requires moisture resistance. It will safeguard against dampness and the effects of any unexpected weather conditions.
- Plywood is known to be durable, and capable of withstanding extreme weather conditions and stress.
Limitations
Plywood despite its many benefits does have some limitations. One of the main limitations of plywood is that it can become damaged due to water exposure for a long time, especially if not treated properly or used in areas prone to moisture. This can result in warping, swelling, or cracking of the material, making it less functional and potentially unsightly.
Another limitation is that the thin veneers used to make plywood can be prone to splitting or delaminating if not handled carefully or if subjected to high stress. Furthermore, plywood is not as strong as other solid wood types, so it is unsuitable for some construction applications or heavy-duty furniture pieces.
Finally, the edges of plywood can become frayed or damaged if not properly finished or covered. Consider these limitations when deciding whether to use plywood in a project and ensure you take precautions to ensure its longevity and functionality.
When To Use Plywood
Plywood is an ideal material for subfloors in construction due to its exceptional strength and stability. In some cases, it can even be used as the finished floor. It is also an affordable and aesthetically pleasing option when it comes to wall paneling.
The engineered wood is great for those looking for something that is moisture-resistant and suitable for decking roofs. It’s also one of the most versatile materials when it comes to making furniture – from bookcases to dressers and many more.
Additionally, the engineered wood has a smooth finish and its wide variety of uses makes it popular amongst crafters when it comes to making decorative items.
The strength and incredible lightness of plywood make it an ideal material for constructing shelves, especially in closets where space is at a premium. This versatile material can be cut into any shape or size so it is a perfect solution for creating stylish yet durable shelving.
When Not To Use Plywood
Plywood may not necessarily be the best choice for every task, so be sure to research and compare alternatives before making a decision.
While the wood is moisture-resistant, it isn’t waterproof – and it can warp if exposed to wet/humid conditions for too long. As a result, it is not recommended for use in high-moisture environments such as basements or exterior surfaces where it will be constantly exposed to rain or snow.
For exterior purposes, plywood can be a great choice but requires adequate treatment and protection from the elements to prevent warping and cracking.
MDF Vs Plywood Comparison
Both materials have their own unique strengths and limitations. The right choice for you will depend on the specific needs of your project.
Below is a comparison of MDF and plywood in these key areas: durability and strength, cost-effectiveness, aesthetics and versatility, and environmental impact.
1. Durability & Strength
In terms of durability and strength, plywood is the clear winner. It is made from thin layers of veneer glued together with the grain of each layer running in opposite directions. This cross-grain construction makes plywood incredibly strong and resistant to cracking and splitting.
On the other hand, MDF is made from fine wood fibers that are compressed and glued together under high pressure. While MDF is also strong, it is more prone to warping, swelling, and cracking.
2. Cost-Effectiveness
When it comes to price, MDF is the more budget-friendly option; it is cheaper to produce than plywood. While plywood is often used in high-end projects where strength is needed, MDF is more commonly used in projects where cost is a more significant concern.
That being said, if you are willing to pay a bit more for the added durability and strength of plywood, it can be an excellent investment.
3. Aesthetics & Versatility
MDF has a smooth surface for painting. Hence, it is extremely popular for furniture and cabinetry as it provides a beautiful look that can last for years.
Plywood, on the other hand, has a natural grain that gives it a more organic look. It is therefore better for decorative accents such as wall panels and trim.
Additionally, plywood can be cut into a variety of shapes and sizes which adds to its versatility.
4. Environmental Impact
When it comes to environmental impact, both materials are eco-friendly.
MDF is made from wood fibers that are often a byproduct of other manufacturing processes. This eliminates the need to cut down more trees for production. However, the glue used in MDF production contains formaldehyde which can be harmful to the environment and human health.
Plywood, on the other hand, is made from thin veneers that are often harvested from sustainably managed forests. Choosing plywood made with locally sourced woods over imported ones would significantly reduce your carbon footprint.
Final Thoughts
When selecting between MDF and plywood, consider all of the factors involved as there is no single solution that works for everyone. It is essential to take into account multiple aspects before settling on your final decision.
MDF is more cost-effective than plywood but is also more susceptible to moisture damage and warping. Alternately, plywood has a higher strength-to-weight ratio, is moisture resistant, and is more suitable for use in damp environments. In terms of aesthetics, MDF has a smoother surface while plywood offers a more natural and textured appearance.
Also, put the environment in which your wood furniture will be used into consideration. For example, MDF is best used for interior applications where it won’t be exposed to moisture or humidity, while plywood is a better choice for exterior applications.
To make an informed choice, compare the benefits and limitations of each material and take into account the environmental impact of each.